What is a Paddle Dryer and How Does It Work?
Discover how JexDry's paddle dryer efficiently removes moisture through conduction heating & agitation. As a leading paddle dryer manufacturer, we ensure uniform drying, low energy costs & minimal maintenance. Solve your industrial drying challenges with us!
3/25/202511 min read
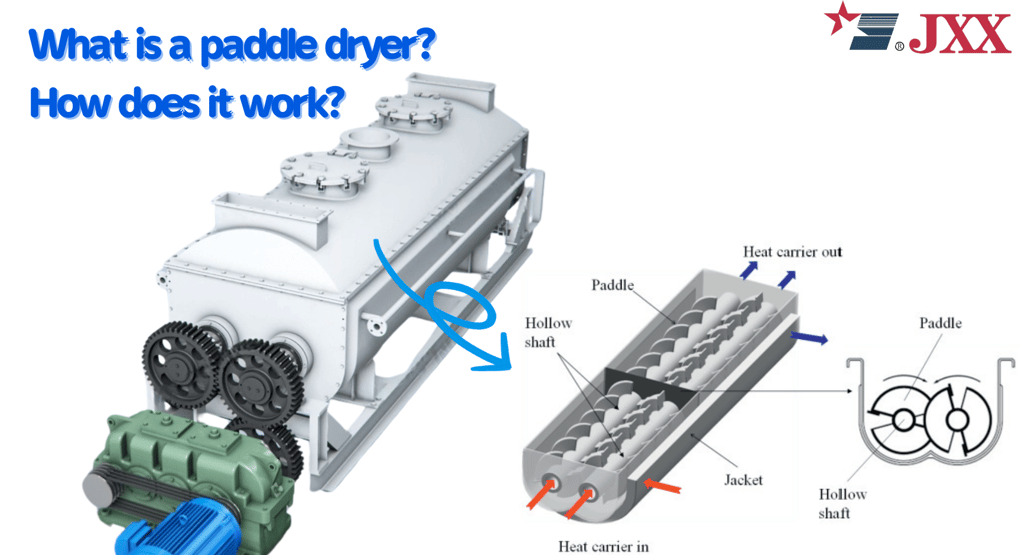
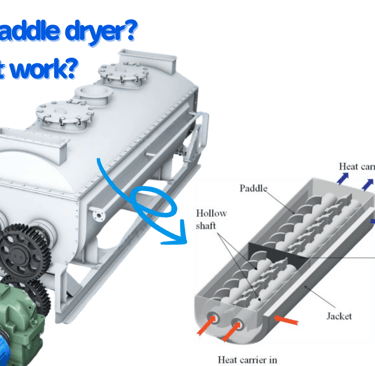
Paddle dryers are revolutionizing industrial drying processes, offering unmatched efficiency for materials like sludge, chemicals, and minerals. But how exactly do these machines work, and why should manufacturers choose JexDry’s advanced paddle drying solutions? This guide breaks down the science behind paddle dryers, their advantages, and how JexDry’s patented technology delivers 30% faster drying times than conventional systems.
A paddle dryer uses rotating hollow paddles and a heated jacket to transfer thermal energy directly to materials, ensuring uniform drying without overheating. Its modular design allows customization for sludge, powders, or granules, while energy recovery systems slash operational costs by up to 30%.
Before diving into the technical details, let’s explore the key questions this article answers:
Table of Contents
1: What Is a Paddle Dryer ?
A paddle dryer is a horizontal, cylindrical machine with hollow shafts and wedge-shaped paddles. Heat transfers through the paddles and jacketed walls, enabling indirect drying. This design minimizes thermal degradation and suits materials like sludge, powders, and pastes.
The process begins when wet material enters the dryer through an inlet. Heated paddles (100–200°C) continuously mix the product, ensuring uniform heat distribution. Moisture evaporates through a vent, leaving behind dry, free-flowing powder.
Paddle dryer key components include hollow paddles and a jacketed shell for 90%+ thermal efficiency via conduction heating, rotating shafts enabling axial-radial mixing with self-cleaning to prevent buildup, an airtight housing maintaining vacuum/inert environments for continuous operation, and emission control systems capturing >95% fine particles and solvents to ensure environmental compliance.Key components include:
1.Thermal Exchange System
Hollow Paddles:
Wedge-shaped blades circulating steam/thermal oil for direct heat transfer.Jacketed Shell:
Double-walled design with 30% more heating surface.Function: Achieves 90%+ thermal efficiency and prevents material degradation.
2. Agitation System
Rotating Shafts:
Drives paddles for axial-radial mixing (3-25 RPM).Self-Cleaning Design:
Eliminates buildup in sticky materials (≤15,000 cP).Result: Uniform moisture distribution (CV≤0.05).
3. Sealed Structure
Airtight Housing:
Maintains vacuum/inert gas environments.Discharge Valves:
Rotary airlocks for continuous operation.Compliance: ASME/FDA-certified for pharma/chemical use.
4. Emission Control
Cyclone Separators:
Capture >95% fine particles.Condensers:
Recover 95% solvents (VOC emissions <50 mg/Nm³).
This component ecosystem achieves 90%+ heat transfer efficiency - 40% higher than rotary dryers - while handling materials from pharmaceutical powders to high-viscosity sludges (15,000 cP).
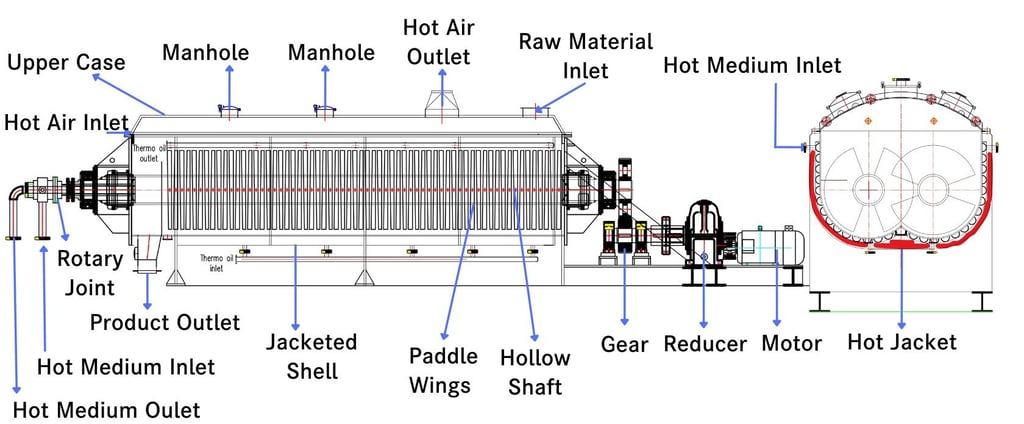
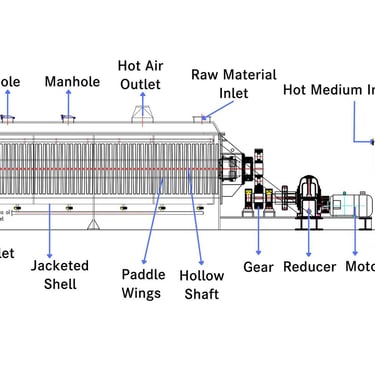
2: How Does It Work?

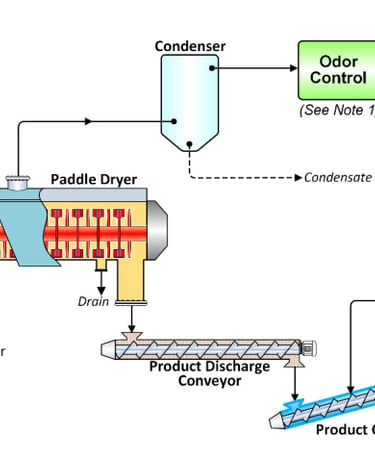
Paddle dryers utilize indirect conduction heating to efficiently process challenging materials like sludges, pastes, and heat-sensitive compounds. This method achieves significantly higher thermal efficiency than conventional dryers while preventing product degradation. Below are the four critical operational stages:
Phase 1: Precision Material Feeding
Solving clogging and inconsistent feed issues
Wet materials enter via tapered inlets and screw conveyors, preventing blockages even with sticky substances (e.g., pharmaceutical intermediates)
Feed rates auto-calibrate to viscosity and moisture content (30-80% range)
Industry impact: Eliminates 90% of sludge feeding downtime in waste treatment plants
Phase 2: Dual-Path Indirect Heating
Ensuring zero contamination + thermal efficiency
Jacketed W-shell design increases heating surface area by 35% vs. cylindrical dryers
Hollow paddles/shafts circulate steam/thermal oil (120-320°C) for direct conduction
Critical advantage: Complete separation from combustion gases meets cGMP/FDA standards
Phase 3: Self-Cleaning Agitation
Preventing buildup and ensuring uniform drying
Counter-rotating shafts (3-25 RPM) drive wedge-shaped paddles
Generates shear forces that continuously scrape heated surfaces
Creates axial-radial material flow for ±0.5% moisture uniformity
Phase 4: Phase-Driven Moisture Removal
Gentle processing for sensitive materials
Plastic Phase: Low-temperature softening
Shearing Phase: Capillary structure breakdown
Granular Phase: Vacuum-assisted (0.1-1 bar) deep drying
Innovation: 30% faster drying than rotary systems while preserving probiotics/vaccine viability
Phase 5: Sealed Discharge & Emission Control
Meeting strict environmental compliance
Airlock valves discharge product under inert atmosphere
Cyclone separators capture 99% particulates (>5μm)
Condensers recover >95% solvents (VOC emissions <50 mg/Nm³)
Output quality: A-grade biosolids ready for reuse
Phase 6: Industry-Specific Optimization
Solving sector-specific pain points
Pharma: 316L stainless steel + SIP sterilization
Food: Nitrogen atmosphere for flavor retention
Hazardous Waste: ATEX-certified explosion prevention
3. Paddle vs. Rotary Dryer: Performance Showdown
4. Heating Medium Guide: Fueling Your Drying Process
Types of heating medium
Paddle dryers use several types of heating mediums. The most common options include steam, thermal oil, and hot water. Each type has unique properties that affect drying performance.
Steam
Steam is the most used heating medium in paddle dryers. Many factories pick steam because it gives steady and even heat. Steam moves through the jacket and hollow shafts inside the dryer. The hot parts send heat to the wet material. This dries the product without using flames or blowing hot air right on it.
Engineers like steam because they can control the temperature well. Workers can change the steam pressure to make it hotter or cooler. This helps when drying things that need gentle care. Steam spreads heat fast over all the surfaces. This makes the dryer work well and stops hot spots.
Note: Steam systems need a boiler and good pipes. Checking the system often keeps it safe and working right.
Advantages of Using Steam:
Keeps temperature steady
Moves heat quickly
Works well for gentle products
Easy to adjust
Disadvantages:
Needs a boiler to work
Needs regular check-ups
Thermic Fluid
Thermic fluid, also called thermal oil, is another common heating medium. Factories use thermic fluid when they need more heat than steam can give. The oil moves through the dryer’s jacket and shafts. It gives steady heat to the material inside.
Thermic fluid systems do not need high pressure to work. This makes them safer in some places. The oil does not turn into steam and go away. It can get hotter than 300°C (572°F). This helps when drying tough or heat-proof materials.
Workers must watch the oil to make sure it stays good. Over time, the oil can get old and not work as well. Checking and changing the oil keeps the system running smoothly.
Hot Air
Hot air can also heat paddle dryers, but it is not used as much as steam or oil. In this way, a blower pushes warm air through the dryer’s jacket or special paths. The air heats the surfaces that touch the material.
Hot air works best for things that do not need careful temperature control. It is good for materials that can handle some air moving around and will not get dirty. Hot air systems cost less to set up and fix. But, they may not heat as evenly as steam or oil.
Tip: Hot air heating is good for easy drying jobs and saves money on equipment.
Benefits of Hot Air:
Costs less to install
Simple to use
No need for boilers or oil pumps
Limitations:
Not as easy to control the temperature
Not good for gentle or sticky materials
Indirect thermal drying technology, which paddle dryers use, transfers heat from these mediums through metal surfaces. The material never touches the heating medium. This design keeps energy loss low and system thermal efficiency high. The heat medium recycles within the system, so very little heat escapes. Paddle dryers with hollow blades and shafts increase the heat transfer area. This setup shortens drying time and reduces equipment size. As a result, paddle dryers use less energy and achieve high thermal efficiency.
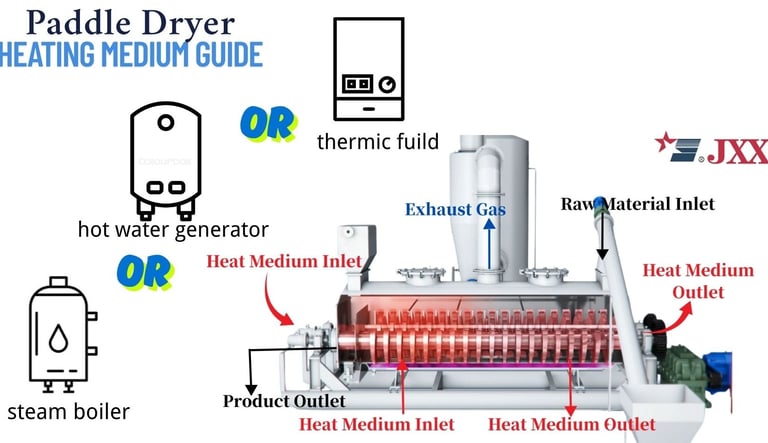
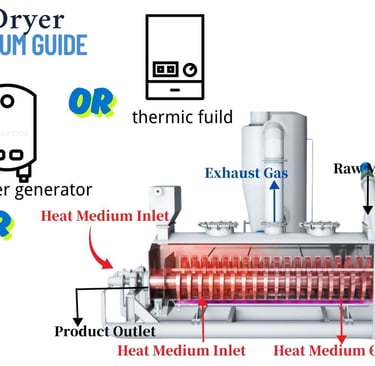
5. What Materials Can Paddle Dryers Process? Industry-Specific Solutions for Critical Drying Challenges
Paddle dryers solve complex industrial drying problems across sectors by handling high-viscosity sludges, heat-sensitive compounds, and sticky byproducts that conventional dryers cannot process efficiently.Paddle dryers use several types of heating mediums. The most common options include steam, thermal oil, and hot water. Each type has unique properties that affect drying performance.
1.Environmental Protection Industry
JexDry paddle dryers are widely used in the environmental industry for the efficient drying of various sludge types, making them a versatile and sustainable solution for waste management. These dryers are particularly effective in reducing the volume of sludge, which significantly lowers transportation and disposal costs. They are suitable for drying a wide range of environmental materials, including:
Municipal sludge
Industrial sludge
Paper sludge
Biogas residues
Drilling mud
Biomass
Digest manure
Pharmaceutical waste
Sugar industry waste
Coal ash
Key advantages include:
Drying through the plastic phase
= no back-mixingUniform product treatment
= perfect hygienizationEnergy efficient
Highest flexibility on sludge types
Minimal off-gasses to treat
Low mechanical speeds / low wear
Compact design and plant layout
Class A biomass production
Safety features
Closed system
No oxygen during process
O2 and CO monitoring
Water spray
No need for explosion panels
These features make paddle dryers an ideal choice for sludge drying in the environmental industry, offering hygienic, efficient, and safe processing with plug flow, no sweep gas, and vacuum compatibility.
2.Chemical Industry
JexDry paddle dryers are widely used in the chemical industry for the safe and efficient drying of various chemical products. Fully enclosed operation ensures the safe treatment of chemical products, and sometimes vapors are diluted with heated air or inert gas to maintain a sufficiently low dewpoint and prevent condensation. A special version of the paddle dryer is available for the crystallization and drying of polyethylene terephthalate (PET), offering degradation-free processing and a narrow residence time distribution.
Special attention is paid to ensuring a tight seal to prevent solvent loss. Solvent recovery is enhanced by maintaining a high concentration of solvent in the exhaust vapor, which can be recycled and heated as sweep gas. Pressure control is achieved through a small gas bleed.
Key applications in the chemical industry include:
Polymers (e.g., PET, SAP, PA)
Gypsum
Minerals
Metal powders
Advantages of Paddle Dryers in the Chemical Industry:
Good plug flow
Fully continuous operation
High capacities
High heat transfer
Excellent sealing to prevent solvent loss
Solvent recovery and gas recycling
Low maintenance and energy consumption
High flexibility for different chemical products
Compact design and plant layout
Paddle dryers are a reliable and efficient solution for chemical drying, particularly for polymers, minerals, and metal powders, offering high heat transfer, plug flow, and degradation-free processing.
3.Food Industry
JexDry paddle dryers are widely used in the food industry for the efficient and hygienic drying of various food products, making them a versatile solution for maintaining product quality and safety. These dryers are particularly suitable for materials such as:
Milk
Starch
Cocoa flour
Sugar
All powders/granules
Key Advantages of Paddle Dryers in the Food Industry:
Plug flow – Ensures uniform drying and minimizes contamination risks
No sweep gas – Prevents introduction of external contaminants
Vacuum compatibility – Allows for low-temperature drying to preserve product quality
Hygienic design – Reduces cross-contamination and supports CIP (Clean-in-Place) procedures
Wedge-shaped paddles – Promote even mixing and heat transfer
Closed system – Minimizes exposure to air and contaminants
High efficiency – Achieves rapid and uniform drying
Compact structure – Suitable for small to medium-scale food production
Low maintenance – Easy to clean and operate
Consistent output – Ensures product quality and compliance with food safety standards
Paddle dryers are essential in the food industry for drying milk, starch, cocoa flour, sugar, and other powders/granules, offering hygienic, efficient, and safe processing with plug flow, no sweep gas, and vacuum compatibility.
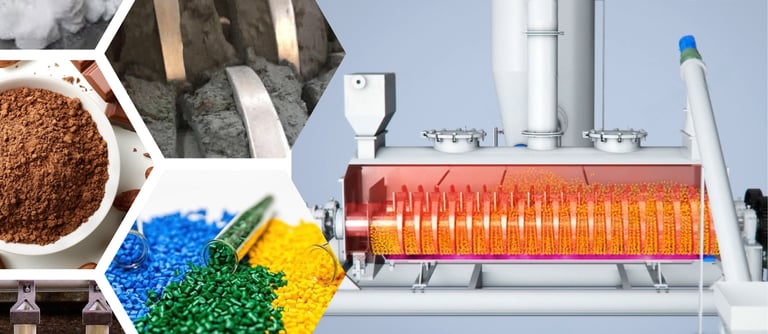
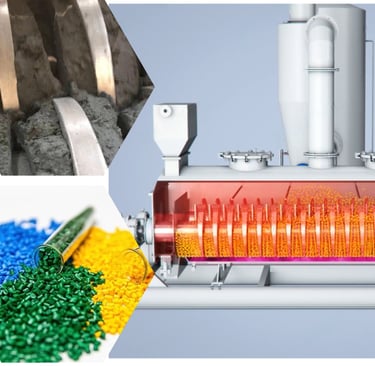
6.What Should You Consider When Choosing a Paddle Dryer for Your Specific Material?
When selecting a paddle dryer for specific materials, it is essential to evaluate multiple factors to ensure the equipment meets the operational, material, and environmental requirements. Below is a detailed step-by-step breakdown of the key considerations:
Material Properties
Understanding the physical and chemical properties of the material to be dried is critical.Moisture Content: Determine both the initial moisture content and the desired final moisture level. Materials with high moisture content may require longer drying times or higher heat input .
Particle Size and Density: The size, shape, and density of particles influence how they interact with the paddles and heat transfer surfaces.
Heat Sensitivity: Some materials degrade, melt, or react chemically when exposed to high temperatures. For such materials, low-temperature drying or vacuum paddle dryers may be necessary.
Viscosity and Stickiness: Sticky or viscous materials can adhere to surfaces, requiring self-cleaning mechanisms in the dryer design.
Corrosiveness and Toxicity: If the material is corrosive or toxic, corrosion-resistant materials (e.g., stainless steel) should be used in construction.
Drying Requirements
The specific drying process requirements must align with the capabilities of the paddle dryer.Drying Curve Characteristics: Analyze whether drying occurs at a constant rate (surface moisture removal) or falling rate (internal moisture diffusion). This affects residence time and temperature settings.
Final Product Quality: Ensure that the paddle dryer can achieve uniform drying without degrading product quality (e.g., avoiding thermal decomposition).
Batch vs Continuous Operation: Decide whether batch processing or continuous operation suits your production needs .
Heat Source Availability
The type of heating medium available impacts operational efficiency and cost.
Heating Medium Options: Paddle dryers can use steam, hot water, thermal oil, or other mediums. Choose based on availability and cost-effectiveness in your facility.
Temperature Range: Ensure compatibility between the heat source’s temperature range (-40°C to 320°C) and material requirements.
Capacity Requirements
The volume of material to be processed determines the size and configuration of the paddle dryer.Throughput Volume: Calculate daily production needs to select an appropriately sized dryer.
Number of Shafts: Larger capacities may require two-shaft or four-shaft designs for efficient mixing and heat transfer.
Energy Efficiency
Energy consumption plays a significant role in operational costs over time.Indirect Heating Efficiency: Paddle dryers use indirect conduction heating with minimal heat loss due to insulation layers.
Waste Heat Recovery Systems: Consider systems that recover waste heat for reuse in other processes.
Material Handling Characteristics
How materials behave during processing impacts equipment design and performance.Flow Behavior: Materials with high viscosity or stickiness may require special paddling mechanisms to ensure even mixing and prevent clogging.
Material Flow Rate: The rate at which material is fed into the dryer affects the required paddle speed and residence time.
Material Adhesion: Sticky materials may require additional measures to prevent adhesion to the dryer walls or paddles.
Environmental and Safety Considerations
Emissions and Waste: Ensure that the dryer meets local environmental regulations regarding emissions, noise, and waste management.
Safety Standards: Choose materials and designs that comply with safety standards, especially for toxic or flammable materials.
Explosion Protection: If the material is explosive, consider the need for explosion-proof enclosures or inert gas protection systems.
Installation and Maintenance
Space Requirements: Ensure the dryer fits within the available installation space and allows for proper access for maintenance.
Maintenance Accessibility: Choose a design that facilitates easy cleaning, inspection, and part replacement to reduce downtime and maintenance costs.
Cost and ROI
Initial Investment: Consider the upfront cost of the dryer, including any necessary modifications or upgrades to the production line.
Operational Costs: Evaluate the long-term cost of energy, maintenance, and labor.
Return on Investment (ROI): Calculate the expected ROI based on improved efficiency, reduced waste, and increased product quality.
Supplier and Support
Vendor Reputation: Choose a reliable supplier with a proven track record in the industry.
Technical Support: Ensure the supplier provides adequate technical support, including installation assistance, training, and troubleshooting.
Warranty and Service: Consider the warranty period and availability of after-sales service to ensure long-term reliability.
By carefully evaluating these factors, you can select a paddle dryer that is well-suited to the specific needs of your application, ensuring optimal performance, safety, and cost-effectiveness. Jexdry stands out as a reliable and innovative choice for your drying needs, offering a comprehensive range of solutions tailored to various industries. With a strong focus on customized design, high-quality materials, and advanced technology, Jexdry ensures that each paddle dryer is optimized for the specific properties of the material being processed. Their expertise in material handling, energy efficiency, and environmental compliance makes them a trusted partner for businesses seeking reliable and sustainable drying solutions. Whether you're working in the food, chemical, pharmaceutical, or environmental sectors, Jexdry provides a reliable, efficient, and cost-effective option to meet your operational demands.
Conclusion: Engineering Resilience Into Every Gram
Paddle dryers aren’t just equipment – they’re moisture insurance policies for your raw materials. By choosing Jexdry, you gain:
Decades of Expertise: 25+ years perfecting conduction drying in China’s industrial hub
Future-Proof Tech: AI-optimized drying curves (±0.8°C control)
Zero-Risk Support: Spare parts airlift within 72 hours
Ready to Transform Your Drying Process?
[Free Material Audit] | [WhatsApp: +86 137 7501 3369] |
External Resource Recommendations
Boost Your Drying Efficiency by 30% Talk to Our Engineers Now!
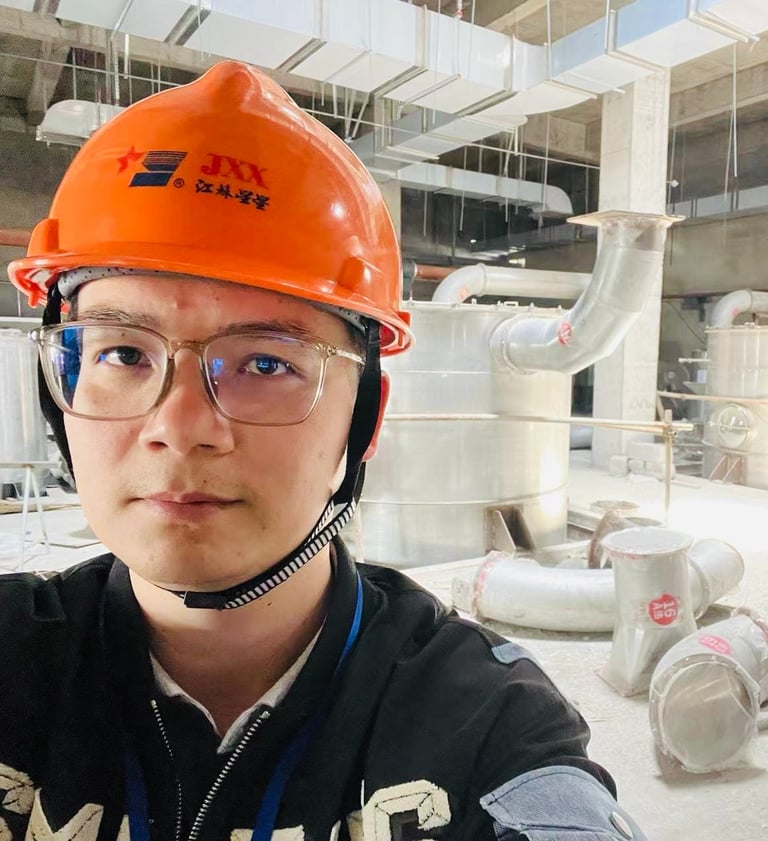
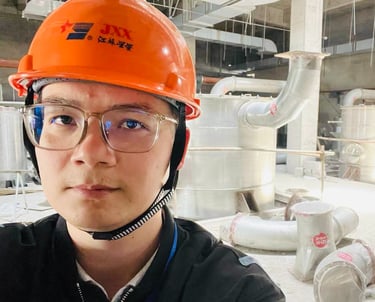
I’m Zar Zha, founder of jexdry.com, a trusted Chinese drying equipment manufacturer rooted in precision engineering since 1998.
As a family-owned business built on three generations of industrial innovation, we specialize in customized drying solutions for demanding industries like food processing, pharmaceuticals, and chemical production.
Over the past 25+ years, we’ve empowered 80+ countries and 200+ global clients—from Fortune 500 food giants to sustainable biofuel startups—to optimize their drying efficiency, reduce energy waste, and scale production safely.
At JexDry, we’re more than equipment suppliers; we’re partners in solving industrial drying challenges. I’m sharing decades of hands-on experience here to help engineers and plant managers master drying technology, avoid costly mistakes, and future-proof their operations.


Feel free to leave your information below, and we’ll get back to you as soon as possible. Alternatively, you can click the green WhatsApp button at the bottom of the page to contact us directly.
JexDry is a family-run business established in 1998, dedicated to providing customers with the most suitable drying equipment to make their production work more efficient, smooth, and environmentally friendly.
Products
Contact
+86-137-7501-3369
© 2024. All rights reserved.